Rockit Global has enjoyed phenomenal growth over its nine years of operation, and ABC has played a significant role in helping achieve this.
Scott Griffin, Rockit Global’s General Manager of Operations, says the ABCpacker programme that records and reports on the traceability of apples from orchard to finished goods “has worked well for us. It’s played a big part in getting Rockit to the stage that it is.”
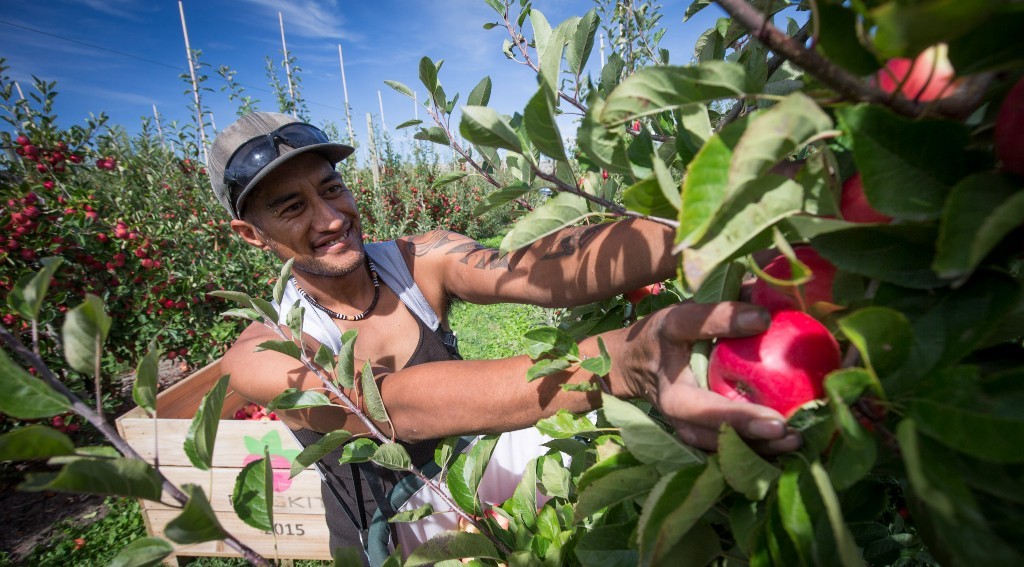
Rockit Global grows, packs and sells miniature apples packed in unique tubes. Its apples are grown under license agreements in New Zealand, Australia, USA, UK, France, Italy, Germany, Spain and Belgium, and are now available year-round in more than 30 countries. Turnover is up over 25 percent year on year.
Formed in 2012, ABC came on board in 2015 to help with packing inventory and traceability through its ABCpacker program. Over the intervening years, the ABC team has worked closely with Rockit Global staff to tailor the software to match the growing business’ needs.
Meeting the regulatory requirements of market access to the ever-expanding number of export countries is “extremely important”, says Sarah Duncan, Quality & Compliance Manager.
“Regulators have a lot of confidence in the system, which makes our lives easier – we know that all our systems are compliant because of the software.”
Kay Lorimer, Logistics Manager, agrees. “Market access is the key for us. The software certainly manages the key requirements we have for market access, which is huge.” She notes that the integration of ABC with NZ Apples and Pears means that shared information “closely flows through into our system”. “Our phenomenal growth has meant our software has had to grow with us,” says Sarah. “ABC is very supportive and proactive in developing the software to meet our needs as we grow.”
The ability to customise ABCpacker is fundamental to its success.
“Everything can be customised, it’s not something that’s a flat package where you can’t make any changes. We can dive in and make it exactly how we want it for all our users, which is a benefit of being able to work closely with them.” Supply Chain Manager, Dennis Paxie, agrees. “The flexibility of the software and the support of the ABC team has made a big difference in helping us grow. An off the shelf solution wouldn’t have enabled this due to the nuances that we need in our sort of operation.”
The “wealth of knowledge” ABC has of the horticulture industry is another plus for the company, Kay says. “They’ve been doing this for a long time, and we are a relatively new company. We know what the problem is, and they know how to solve it. They’ve been there before, seen it before, and know what needs to be done. They offer solutions that we can customise to suit us.” The responsiveness of the ABC team is seen as another strength. “We just pick up the phone and they’re there. We get answers really quickly, and if they need to come back to us, we’re not left hanging for days on end,” says Kay.
Rockit Global’s off-season provides a short window for enhancements to be made to the software, and 2021 has been a big one ahead of its state-of-the-art packhouse, coolstore and office facility in Irongate, Hastings getting into full swing. Having not managed its own fruit storage before meant pallet scanning and other systems needed to be trialled and tested to ensure everything is located where it should be. A full despatch module has integrated the sales and logistics teams to provide better visibility and allocation of fruit into specific markets. The tracking of all packaging elements for the vastly increased packhouse throughput has also been strengthened.
In a separate project, Production Manager, Michael Kelly worked with ABC Software to ensure the company could provide full traceability on fruit for the Japanese market. As fumigation is required, a remote team under his supervision must unpack and then repack the fruit to meet that country’s regulations. “It works exactly as I need it to, and frankly makes my job a lot easier.” During the previous season, tracking had been done manually on spreadsheets, which Michael says, “was extremely difficult”. “We contracted this need to ABC to automate and now it runs seamlessly.”
All agree that working with ABC Software is a pleasant experience, citing good clear communication, responsiveness, and the willingness to “nut things out together”.